Fire Detection and Gas Suppression for Critical Electrical Infrastructure at a West Africa Gold Mine
- FS-Systems
- Mar 23, 2020
- 2 min read
With zero impact on mining operations, our Africa team designed and deployed a robust fire detection and gas suppression system in West Africa within 8 weeks.
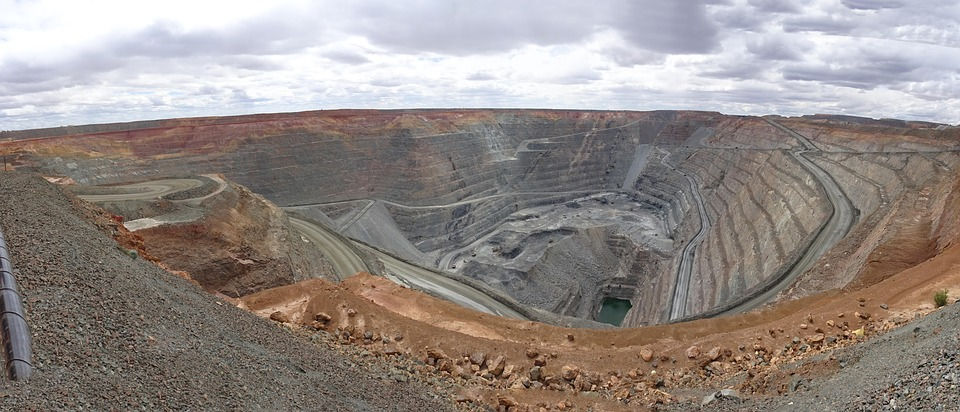
THE BACKGROUND
Headquartered in the Americas, the client is a senior gold producer with five operating gold mines, and numerous exploration and development projects in various countries.
The client realized that fire posed a significant financial risk in both the cost of capital equipment and business continuity to their Surface Open Cast Mine in West Africa. There was also a risk to the lives and safety of personnel on the site.
The mine required an Early Warning Fire Detection System which connected to an Automatic Clean Agent Fire Suppression System. The operation of the system had to be simple and easy enough for an untrained person to understand, whilst still providing high quality protection. The equipment needed to be robust enough to deal with the harsh weather conditions in West Africa and be easy to maintain. The extinguishing gas could not cause damage to the equipment in the protected space or be hazardous to people who may in the area should the system discharge.
The client expected a fully functional Fire Detection and Suppression System designed in accordance with prevailing standards. The installation of the system needed to have zero impact on ongoing mining operations and the location of system devices could only take up as small a footprint in the protected spaces as possible.
THE SOLUTION
The client had a long-standing relationship with FS Systems International and was familiar with the quality of their work on previous projects.
The Fire & Life Safety Team engaged with the client’s Emergency Response Coordinator, Plant Manager and Head of Electrical Maintenance to fully understand the scope of the challenge and discuss viable solutions. Twelve Critical Electrical Infrastructure rooms were identified as being in scope for the project.
The solution was developed in four weeks and deployed in eight weeks. An ASD early warning smoke detection system combined with a conventional gas control panel to which optical smoke detectors are connected in double knock configuration, was identified as a suitable detection solution for each protected area. A pre-engineered FM200 gas suppression system with electrical actuation was identified as a suitable fire extinguishing system. A bespoke integration pack was developed and deployed for the customer to interface all systems into their on-site PLC system. Furthermore, linear heat detection cable was fitted to all cable ladders underneath the structures to provide warning of possible fires in cable tunnels that may approach the protected spaces.
SUMMARY OF PRODUCTS AND RESOURCES
9 Vesda VLF ASD units, 12 Advanced Electronics TC3001 Control Panels, around 150 Conventional Smoke Detectors, 40 Sounder Beacons, 12 Fire Bells, 1km Linear Heat Detection Cable, 8km PH30 Cable and 25 FM200 Cylinders containing around 4 tons of FM200.
THE CONCLUSION
The client was happy with performance across all aspects of the project. At the time of writing this report the systems have performed to specification and have been fault free for over 12 months.
Comments